Reasons Why Industrial Coatings Are Important
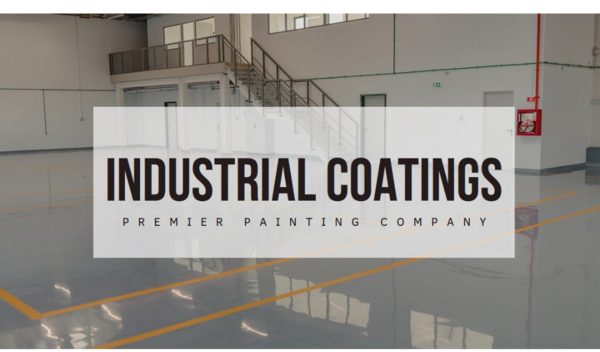
Ambient, maintenance and safety are becoming top concerns of organisations. That's because the industry is booming, where competition is fierce. Companies have taken various measures to protect their commercial-industrial properties and continue thriving in the game, but industrial coatings are still the most overlooked today. The main reason is that many of us are unaware of what industrial coatings are and their purposes.
For instance, as a facility and property manager, your job requires you to decide how to maintain and improve the look and performance of your properties. Sometimes this involves painting and coating. So what is the difference?
The primary purpose of a paint job is to improve the property's aesthetic value. Paint can be applied to a wide variety of surfaces using various application techniques. While some protective qualities come with paint, that is not a paint job's real purpose. The result of painting is any surface that is temporarily better, more vibrant, cleaner, or newer than before painting.
What paint can't do is where the industrial coating comes in; it protects and performs. In other words, industrial coatings are just like paints but with a purpose. Industrial coatings play an essential role in protecting the interests of industries and resisting rust, corrosion, wear and tear.
The final goal depends on the paint system selected. Unlike conventional paint projects, an industrial coating done by a professional painting company is essentially a specialised paint used to protect various substrates, such as concrete or steel. No company can delay their industrial coating maintenance or apply layers to new equipment.
Types of industrial coating
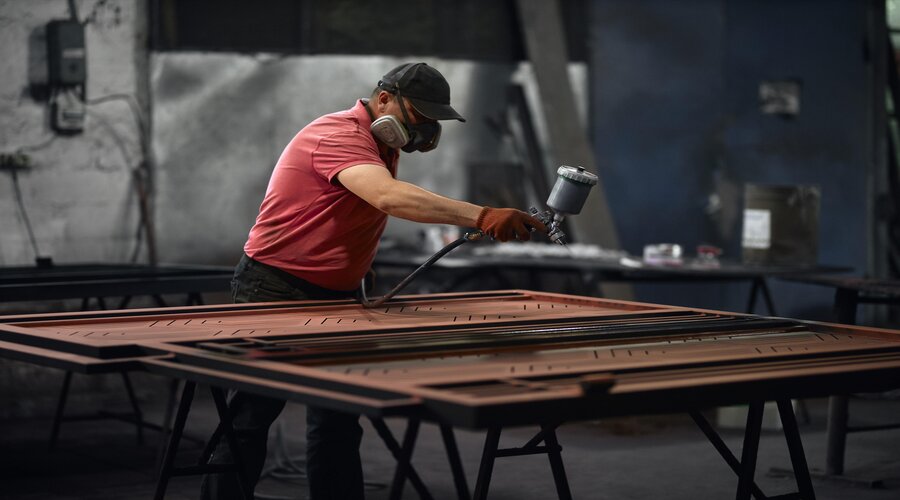
There are many types of industrial coatings. The ideal primer, coating or sealant for your project depends on your application's environment, the type of product you will be storing, and other factors. Knowing the different industrial coatings and their ideal applications will help you achieve the best finish and highest level of protection for your materials every time. Here are four of the most common industrial coatings in use today:
Epoxy coating:
Epoxy coatings effectively resist corrosion, wear and weathering, making them ideal for steel applications located in harsh operating environments.
These coatings are also heat resistant, so they can be used on tanks that hold hot products or are exposed to extreme heat. Their exceptional film thickness enables them to resist bad weather and abrasion.
In contrast, epoxy performs very poorly when exposed to sunlight. For this reason, they are often used for submerged surfaces or those not exposed to direct sunlight. These include steel components inside nuclear power plants and submersible components in water treatment facilities.
Acrylic coatings:
Acrylic industrial protective coatings are commonly used in automotive and architectural applications due to their high gloss and corrosion resistance. This coating is used as a finish for exterior surfaces due to its ability to retain colour despite outdoor exposure. Acrylic coatings are also primers because they can better bond other coatings to the surface. Changing the ratio of additives and binders in acrylic coatings will allow you to tailor their performance to your property specifications.

Zinc-Rich coatings:
Zinc coatings provide a polymeric and electrical barrier, making them highly effective for steel parts requiring correction and wear resistance.
This sturdy protective layer comes from the zinc dust used in the coating and the polyurethane or epoxy adhesive used to create the coating. Zinc particles corrode before the steel surface when exposed to the environment. When zinc dust erodes, it will make a protective film to protect the steel from environmental agents. Inorganic coatings are known to provide better protection but require the surface to be thoroughly cleaned before application.
Polyurethane coatings:
Polyurethane coatings are widely used, often as a top coat, in applications where durability and resistance to abrasion are essential factors to consider.
These coatings create a high-gloss, wear-resistant finish. Because of these characteristics, polyurethane coatings are often used as topcoats for surfaces that need to remain smooth and scratch-free.
Polyurethanes are generally divided into two categories: aliphatic and aromatic coatings. Aliphatic polyurethane coatings offer excellent colour retention and durability under sunlight, making them well-suited to outdoor environments. On the other hand, aromatic polyurethanes are better adapted to flooded environments - they chalk and weather when exposed to sunlight.
How industrial coatings are beneficial for your properties
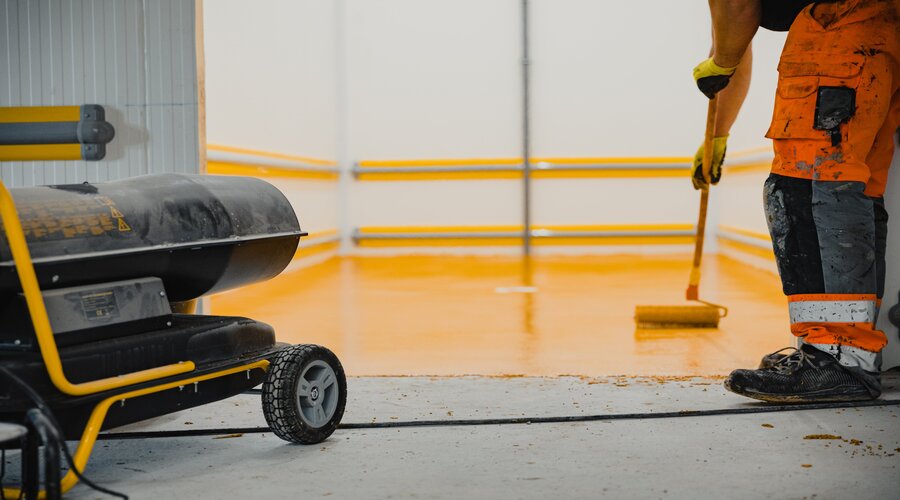
Surface protection
Manufacturing facilities, garages, warehouses, and other operations with heavy machinery and traffic often hire industrial painting company to protect hard concrete or stone floors. Uncoated concrete surfaces are also susceptible to the harmful effects of chemical agents.
If you work in an industrial environment, you already know your equipment wears out on a daily basis. The application of coatings protects various surfaces and their contents so that they can maintain their properties longer. Whether it's acids, caustics, salts or any other chemical, the life span of a concrete floor is dramatically reduced when exposed to these elements. Industrial coatings add an extra layer of protection to all surfaces, improving durability and longevity.
Fire protection
Industrial and commercial properties must take measures against fire. The flame retardant coating prevents flame and heat from spreading in the event of a fire. There are several types of flame retardant coatings, each designed for different applications and purposes. Industrial coatings can provide a passive fire protection solution, making buildings more resistant to fire. These coatings can prevent severe fire damage, slow the spread of flames, and give people time to evacuate safely in the event of a fire.
Corrosion prevention
Another problem in industrial applications is rust or other corrosive debris. Rust and other forms of corrosion can damage machines, equipment and surfaces in industrial environments. The application of industrial coatings by professional commercial painting contractors prevents rust and corrosion from eroding and damaging buildings and equipment.
Often, materials that are hard enough to build machines are also very susceptible to corrosion over time. Sometimes materials passing through these machines cause them to corrode. The only solution is to apply an industrial coating, as it can be designed to create a perfect connection between the machine and its working material. It can withstand the machined material and prevent standard corrosion that can occur simply due to the machine's construction material.
Manufacturing safety
The non-stick industrial coating provides an extra layer of safety in production environments. Some machines may require a non-stick surface on the inside to reduce friction, faster processing, and maintain quality control. Ensuring all surfaces are adequately protected makes work more productive and reduces workplace injuries.
Sometimes you may need to make the surface non-slip or non-stick. Floors are an example of where you need an industrial-strength coating to prevent slippage, especially in areas where a lot of liquid could fall onto the floor. Other machines may require an internal non-stick surface to ensure fast and quality material handling. Industrial coatings are the best way to protect many types of surfaces.
Opt for the professional industrial coatings experts
Industrial coatings are an essential part of any device, so it's crucial that you take the time and research to make sure you have the right coating.
By industry, paints and coatings used for manufacturing, warehousing and other commercial properties must meet stringent health and safety standards. One of the best decisions a business owner can make is contracting with a reputable and knowledgeable industrial coatings contractor who complies with general state building and industry regulations. , federal and federal. Industrial coatings and coatings applications require specialised equipment, experience and training.
As an accredited industrial painting service, Premier Painting Company offers a wide range of industrial coating solutions designed to meet and exceed your expectations. With decades of experience, we have a proven track record of delivering work to your specifications on time and within budget. Tank coatings, pipe coatings, high-temperature coatings and more - we're your one-stop shop for industrial paints and coatings.