Understanding The Industrial Coatings
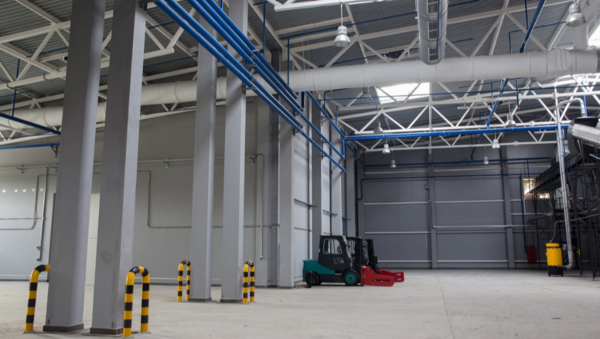
Suppose you have a business where your industrial equipment is central to your investment. In that case, you know that equipment maintenance and protection are the number one priority in your activities.
Industrial coating is basically specialised paint used to protect different substrates, such as concrete or steel. The range of industrial coatings, preparation, and coatings extends from manufacturing facilities, processing plants, and other heavy-duty installations.
This level of service for engineering and special coatings for high performance goes beyond mere aesthetics. That is why business owners and operators must engage with experienced, certified paint contractors who know how to ensure the protection and effectiveness of industrial coatings.
So What Exactly is Industrial Painting or Coating?
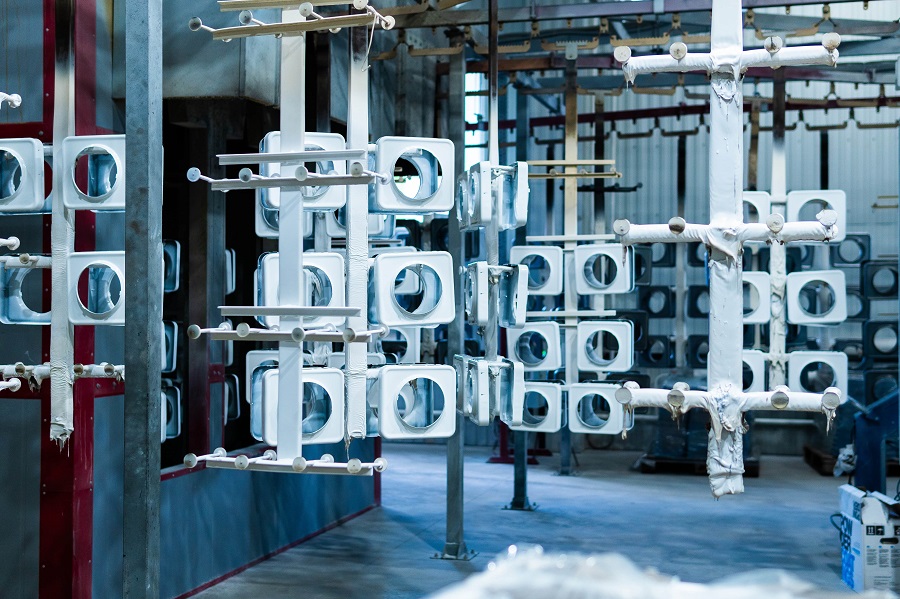
While residential or commercial painting considers the aesthetics associated with the company's finish, it is crucial in commercial painting to create a durable surface that can withstand abuse and lasts longer. Unlike commercial paints for buildings, many companies prefer oil-based paints over latex. Oil-based paints take longer to dry but are more durable and last longer. In addition to traditional varnishes, industrial coatings improve the durability and longevity of the lacquer.
And this is why members of the commercial industry sector rely on various industrial coatings to offer the benefits to their employees, products, and infrastructure that traditional residential coatings cannot.
Industrial coats, also known as maintenance paints, are paints or coatings used to protect industrial components and structures.
The purposes and uses of industrial coatings are vast. The coats are primarily chosen for their protective properties rather than aesthetic quality, but with suitable paints, tools, and techniques- both can also be offered. For example, to create industrial maintenance paints, you can use high-performance epoxy coatings, acrylic primers, varnishes, and varnishes. Dulux accredited industrial painters generally use high-performance epoxy coatings, acrylic primers, and varnishes to develop industrial maintenance paints.
In particular, industrial coatings are well known for their most common use in preventing the corrosion of concrete or steel. Another everyday secondary use is to improve the resistance to fire or other potential problems of these materials. Industrial coatings are used to coat the inside of water tanks and reservoirs to create a safe environment for drinking water and protect them from corrosion. The most frequently used industrial coatings are polymers.
Some examples of polymers used as industrial coatings are epoxy, moisture-cured urethane, polyurethane, and fluoropolymer. Leak prevention and corrosion prevention are still two critical goals of industrial coatings. Still, they are not the only ones- these products offer higher levels of functionality than conventional paints found at your local hardware store.
Different Types of Industrial Paints
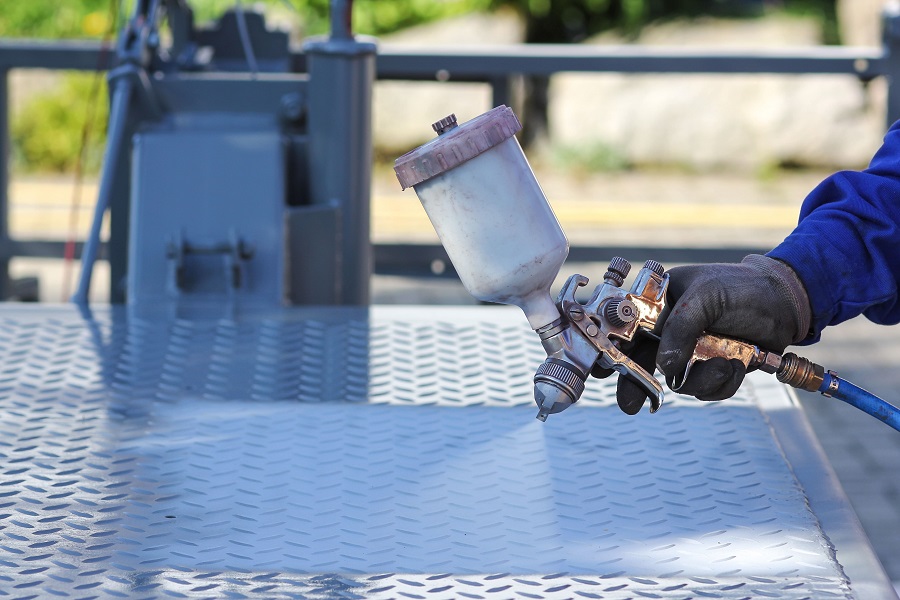
In industrial environments where surfaces are subjected to daily wear and tear and are exposed to physical and chemical attacks, optimum strength, resistance, and durability are guaranteed and achieved over time through residential painting or finishing. Therefore, the correct selection of industrial paints and coatings is essential.
Industrial coatings come in many different forms. Regardless of the type, their primary function is to protect the underlying surface. Here are some of the common types of industrial coatings along with their characteristics and functionalities.
Epoxy Coating System:
These coatings have created many high-performance coating products with excellent film formation and mechanical and chemical properties. In addition, these have a shorter drying time than alkyd paints. As a result, these coatings can be used for industrial painting projects that require maximum protection from normal wear, wear, corrosion, moisture, water, and chemicals.
Many industrial facilities choose epoxy coatings for concrete flooring because of the numerous advantages it provides, which include-
- Versatile to provide a wide variety of different coating properties and also can build film thickness
- Long-lasting, cost-effective, waterproof, and shock-resistant industrial coating choice
- Improved operational safety since they aren’t slippery like polished concrete.
- Increased visibility with its high sheen, reflecting light sources and improving visibility making for a safer working environment.
- Perfect on submerged industrial applications like dip coating or immersion coating, resistant to chemicals and abrasions.
Alkyd Coating:
The term "alkyl" is derived from the words "alcohol" and "acid." It describes the origin of the resin from which the coating is capable of forming a film. Despite not being as durable as polyurethane and epoxy coatings, alkyd resists wear and creates an attractive glossy finish. These coats can be used for interior and exterior surfaces, even those submerged in water or located underground.
Depending on the components incorporated, alkyds can be used for various interior, exterior, underground and underwater applications. These paints use oxygen to complete a chemical reaction to provide a long-lasting finish. However, these coats take longer to dry because oxygen must be dispersed through the coats.
- Widely preferred for high traffic areas such as hallways and playrooms for children
- resistant to stains with a lustrous finish and effortless cleaning
- Coats are not absorbed efficiently and have no risk of discoloration, retaining a uniform sheen for a long time.
Polyurethane Coatings:
Polyurethane itself is a polymer related to a group of chemical compounds known as carbamates. This polymeric material is also thermosetting; in other words, it burns rather than melts when heated. Another feature of polyurethane coatings is their customisability. These coatings can be formulated into glossy, matte, opaque, or transparent.
- Does not contain any VOCs or FCs, requires no complex application systems, and has excellent resilient qualities.
- One of the most versatile polymers in paint formulations due to its low temperature and fast curing properties, physical properties and ease of application.
- Better elasticity also means that polyurethane floors can retain their shape and mechanical properties at temperatures below 1°C.
Metallic Coated Films:
Metallic coated films have a coating or thin metallic film for decorative or functional industrial applications. The metallic film has a metallised layer, appearance, or a thin film coating. Laminated films are made from fibers, sheets, or fabrics bonded or laminated to a metal substrate film to improve strength or other properties. Metallic coatings can be applied by spray, electrochemical, chemical, or mechanical. These coatings are applied to equipment requiring a glossy or shiny appearance and protection from the sun, corrosion, and oxidation.
- Provides scratch resistance, control of friction or adhesion (controlled COF), and release.
- Improves print reception, modifies optical transmittance or reflectivity, and provides decorative characteristics.
- Offers a lifetime cost advantage over traditional protection methods that do not perform well in harsh environments.
How Long Does It Take to Finish an Industrial Coating Project?
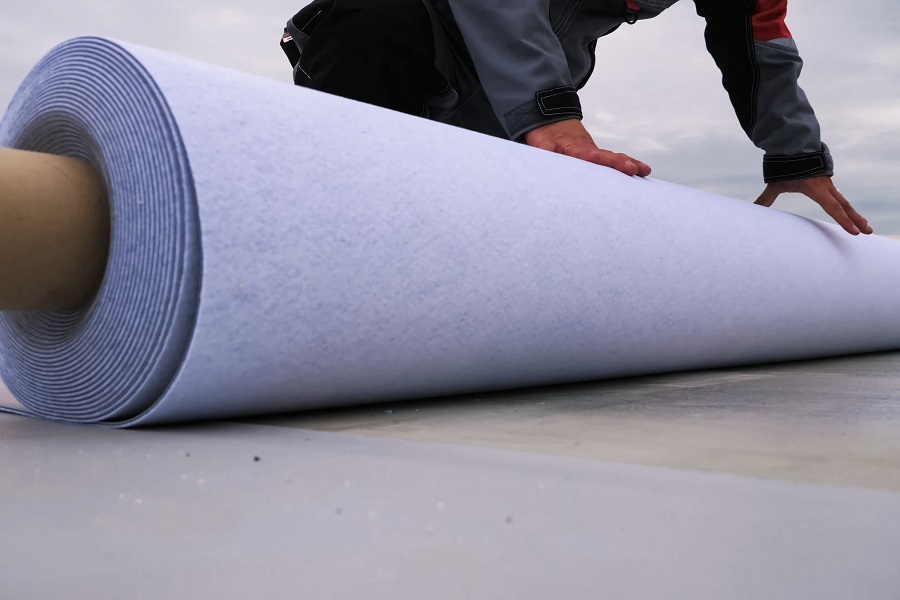
The schedule for a particular project depends on a number of factors, including the required coatings and the accessibility of the area.
Typically, industrial painting professionals can complete a small to medium-sized job in days or weeks. Therefore, progress can be accelerated to meet customer needs, but the project cost estimate will reflect additional personnel or equipment.
It may be necessary to restrict access to the area and divert traffic during project implementation. Many industrial coatings have a “cure” period of 13 days, during which time they will harden and acquire the expected performance properties. During this time, it is essential not to disturb the treated area and maintain it at the temperature specified by the coating manufacturer.
How to Choose a Custom Industrial Coating for Your Project?
Industrial coatings are more than just an aesthetic finish to industrial equipment or primary materials. Instead, industrial coatings are barriers designed to protect components from various damage and harsh environments. Concrete, plastic, and metal materials are often durable in many ways. Still, each base material requires a protective coating that adheres to its surface and protects it from corrosion.
Industrial coatings protect materials and components ranging from infrastructure piping to machinery to floors and other surfaces. These coatings can be applied by brush, spray or dip, with each type of application requiring a careful formulation. The method of using your business of your choice should supplement your production capabilities and create effective instead of congestion.
The key factors include:
Substrate Identification
The ideal industrial coating formulation may require acrylic, urethane, epoxy, or other materials depending on the substrate. Manufacturers also need to consider whether parts are made of a variety of materials and when throughout the manufacturing process, a coat of industrial paint should be applied. Some substrate and coating pairs can also be bridged by using the correct primer or a combination of additives to promote adhesion or improve other properties.
Manufacturers must also consider the unique protections that the substrate requires, such as compliance with food safety regulations, corrosion resistance, etc. Depending on the surface condition and the geometry of the surface, different application methods and materials can yield results superior to other methods. In addition, some substrates are susceptible to changes in composition by various application methods and curing procedures.
Temperature
It is important to think about the temperature to which the coating will be applied, along with the surface temperature. Next, consider the longevity of the product and what service parameters will the coated product see after leaving your facility. Finally, consider the temperatures to which the material will be subjected during the service life of the coated part.
Drying conditions
A common mistake made by manufacturers is when the coating appears to be dry, and they pack the product for shipping, but the film has not fully cured. In this case, durability is affected, and the paint is peeling, rusting, or showing some other form of paint or disappointing product. Again, asking about temperatures to professional industrial painting service in advance makes the coating suitable for dry and general weather conditions.
Lastly,
Most industrial coatings do not require much maintenance beyond regular cleaning. As long as they are appropriately applied in the first place and given time to cure, they are quite complicated.
That's why it's important to hire the right industrial painting service with the right experience to do the job right. If you hire an experienced painter and follow the manufacturer's instructions for long-lasting paint, you'll be happy with your investment.